
December 14, 2018
The Teys Australia cattle hide processing plant at Murgon plans to lift production by 20 per cent recent – and hire a dozen more staff – over the next two years.
A $567,406 expansion at the facility was officially opened by Member for Wide Bay Llew O’Brien on Thursday morning.
The project – to create a sixth “raceway” processing tank and an overhead hide delivery system – was jointly funded by the Federal Government’s Regional Jobs and Investment Package ($267,406) and Teys Australia Murgon Pty Ltd ($300,000).
The raceway is a 100,000 litre brine tank that hides pass through as part of the curing process.
The “Raceway 6” project also provided a boost for Bryan Zelinski Engineering in Murgon, which did all the fabrication work in their workshop.
The massive tank was then transported to the Teys factory by low-loader and lifted into place by two mobile cranes.
More than 13 local tradespeople were engaged to complete the project.
The raceway, which weighs about 140 tonnes at full saturation, sits at the end of a row of five other raceway tanks that can now process about 16,000 hides a week.
“This expansion will increase production and create more employment opportunities, providing a welcome boost to the local economy,” Mr O’Brien said.
Last financial year, the Murgon plant processed 710,000 hides, which arrive chilled from Teys’ abattoirs at Rockhampton, Biloela and Beenleigh.
“Ten per cent of all cattle slaughtered in Australia come through this plant,” Teys Murgon general manager Scott Kapernick said.
The hides end up as the finest leather upholstery in many European prestige vehicles.
The Murgon plant was originally opened by Burnett Valley Ltd in October 1991 as a wet blue tannery.
Teys bought the facility in 2005 and since then the plant has undergone major efficiency upgrades to lessen its environmental footprint.
Hides now leave the plant as brine cured, packed into containers for export.
These days, only one skip of rubbish leaves the plant every week, and a closed loop water system recovers five litres of water from every hide that arrives at the plant.
“We make 180,000 litres of clean water every week,” Scott said.
“We lose more water now through evaporation than we bring into the plant.”
The salt used in the brine process is also recycled – about 70 tonnes a week – following the installation of a $1.6 million salt recovery system in 2013.
The latest expansion will also have flow-on benefits for Murgon on top of the extra jobs.
A 20 per cent increase in capacity means 20 per cent more wooden pallets, which Teys source from The Gumnut Place.
Teys Australia Group Environmental Manager Amelia Simony said the project was just another way that Teys continued to invest in Australian agribusiness.
“The project follows innovation and environmental focus at the site, having recently been recognised as ‘best-in-class’ hides processing in Australia for the closed loop water treatment system and significant waste reduction,” she said.
“Teys have recently made a commitment to support sustainable beef processing by reducing our carbon intensity by 20 per cent and our water intensity by 10 per cent by 2023.
“We also support the red meat industry achieving carbon neutrality by 2030.”

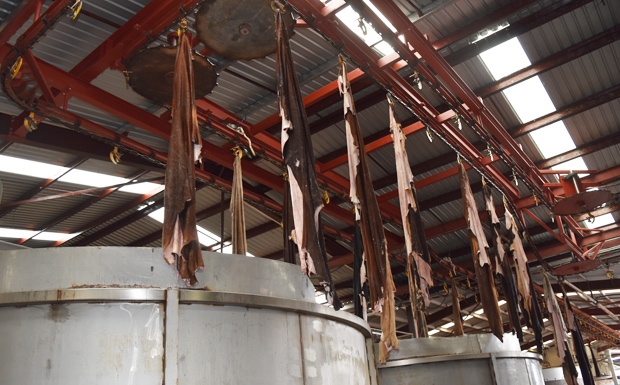
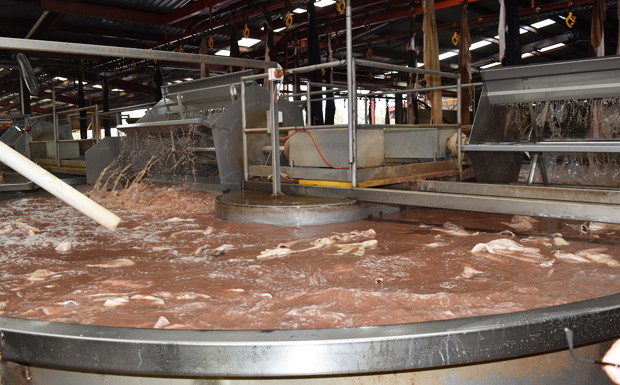
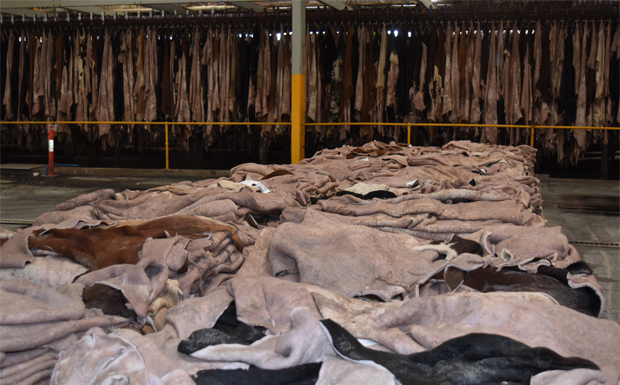
* * *
Teys are very proud of their closed loop water recycling system …
[UPDATED with correction]